With the right catalyst, we could make jet fuel from CO₂
As carbon capture becomes cheaper, new applications may look attractive.
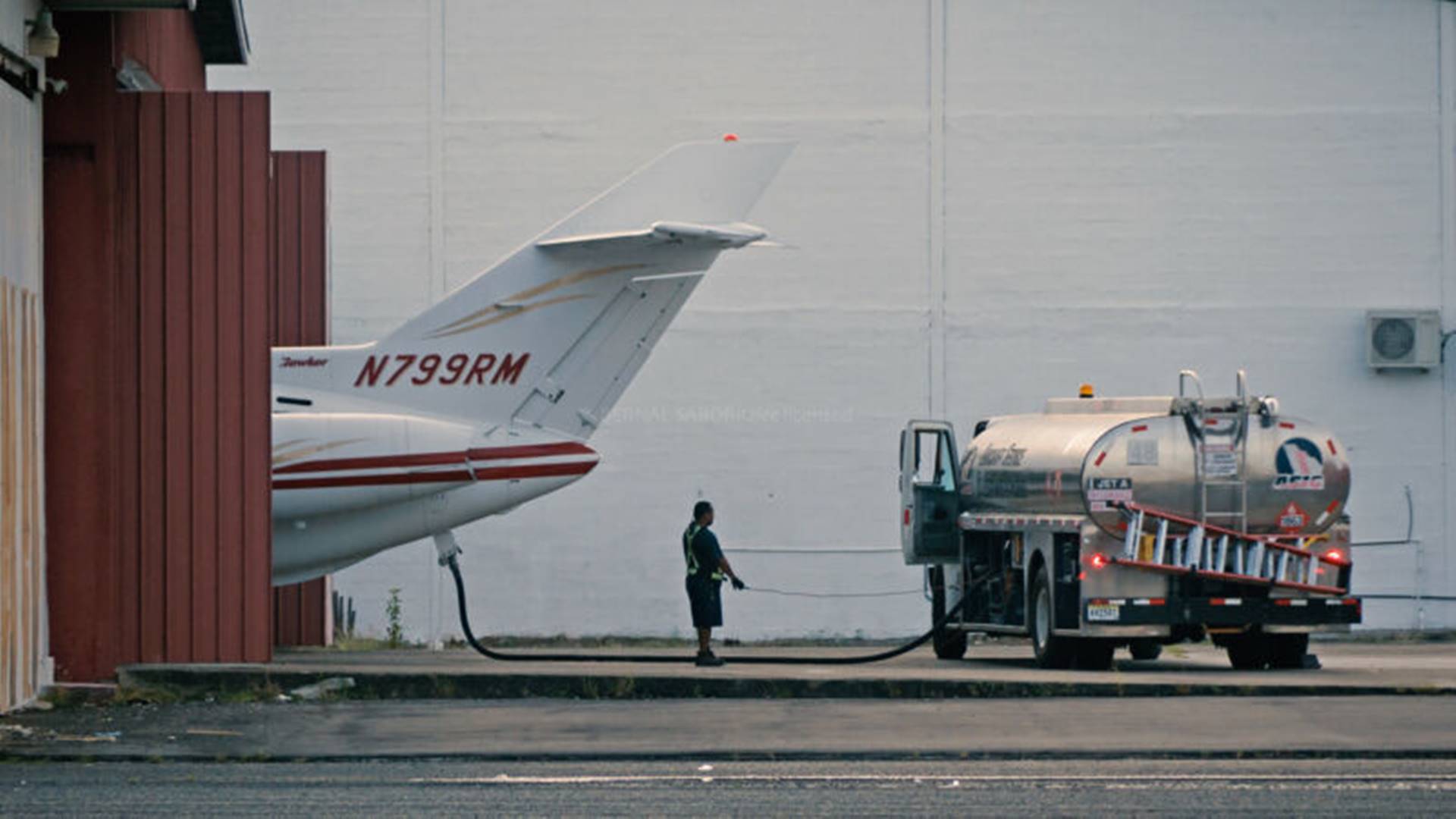
Techniques to convert atmospheric CO2 into fuel offer a climate-friendly alternative to fossil fuel use – they may release CO2 into the air when burned, but there is no net change. This includes biofuel cultures, but can also extend to industrial processes in which CO2 is directly involved. As processes that capture CO2 from the ambient air become more economical, so too will the potential value of this CO2 as a resource for fuel.
There are a few ways to make fuel, but all of them require considerable energy as CO2 is a stable molecule – the reverse of that Combustion reaction to produce a new fuel is not free. But there is an additional challenge: designing a process that is precisely tailored to the type of fuel you want.
One way to do this is with a catalyst – a substance that controls chemical reactions without being consumed. b With the help of a catalyst, captured CO2 plus hydrogen gas can mainly be converted into methane. Another catalyst could shift the primary product towards the larger molecules of liquid fuels.
A new study by Benzhen Yao at Oxford University describes a new catalyst that specializes in the production of the long-chain hydrocarbons used in jet fuel.
Related Posts
The numbers
This catalyst is an iron-manganese-potassium material – nothing too exotic. In testing, only five percent of the converted CO2 ended up as carbon monoxide and 10 percent ended up as methane, while nearly half became long-chain hydrocarbons in the jet fuel range (8-16 carbons). Compared to other catalysts tested in previous studies, that’s a much better departure in the jet fuel range. And of the 2-4 carbon hydrocarbons produced, it favors alkenes over alkanes, which means more carbon-carbon bonds and fewer carbon-hydrogen bonds. both propylene and propane, for example. These are useful raw materials for things like plastics.
The catalyst provides sites to host reactions, which influences the product. Here, that mostly happens in an iron-carbon ore that is converted to and from iron oxide. One form helps CO2 molecules to react with hydrogen, while the other helps the resulting carbon monoxide molecules react with hydrogen to form hydrocarbons.
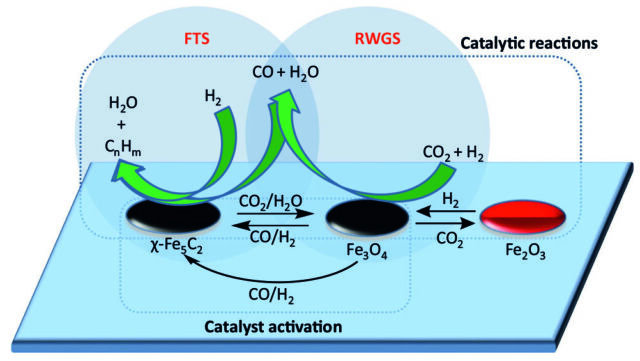
The method of making the catalyst results be in the materials was combined with an organic compound that burns while everything is kept at 350 ° C for several hours. The combustion reaction helps iron, manganese, and potassium from the correct minerals, and leaves some carbon behind. Experiments with a similar catalyst material done in a different way were much less effective. changes, which means it might have to regenerate at some point. As before its first use, that can be done with high temperatures in the presence of hydrogen and carbon monoxide, restoring the mineral forms in the catalyst.
As part of a process real. global system, this would be connected to a CO2 capture plant and electrolysis device that splits water to produce hydrogen gas. Products could be separated and processed as needed
Obviously, this study only relates to understanding what type of catalyst to use, and there is no economic analysis of the fuel production operation here. There are many energy inputs to this process, especially when compared to traditional oil production. Petroleum-based fuels add to the CO2 in the atmosphere, air-based fuels could add very little (or nothing, depending on where the required energy comes from). And this also comes with the option of tailoring the types of hydrocarbons that you produce, rather than just working with whatever comes out of the ground.
Arstechnica.com / TechConflict.Com